2025.5.14
Additive Manufacturingとは?製造現場を変える積層造形の可能性
目次
1. AMの基本:Additive Manufacturingとは何か
Additive Manufacturing(AM)は、単なる3Dプリント技術にとどまらず、設計から製造までを含む革新的な製造アプローチとして注目されています。近年では、プロトタイピング用途に限らず、最終製品の製造にも活用されるケースが増え、製造業全体に大きな変革をもたらしています。ここではまず、AMがどのような技術であるかを基本から整理し、その定義や背景について詳しく解説します。その上で、従来の切削加工や鋳造といった製造手法との違いに触れ、AMならではの優位性や適応範囲を整理していきます。
1-1. 積層造形の定義と背景
Additive Manufacturing(以下、AM)とは、材料を一層ずつ積み重ねることで立体物を造形する「積層造形技術」の総称です。従来の切削や鋳造などの加工方法とは異なり、材料を“削る”のではなく“積む”ことで形を作るのが特徴です。
AMは、米国規格協会ASTMによって「3Dモデルデータを基に材料を層状に堆積させて物体を作るプロセス」と定義されており、一般には3Dプリンター技術として知られています。かつては試作品を短時間で製作する技術「Rapid Prototyping(RP)」として使われていましたが、近年は最終製品の製造にも活用されるようになり、製造技術として再定義されるようになりました。
AMと3Dプリンターは密接に関係していますが、厳密には次のように区別されます。3Dプリンターは積層造形を行う装置そのものであり、AMはその活用方法や設計手法、材料選定、製造工程まで含んだ広い概念です。
1-2. 従来の加工方法(切削、鋳造など)との違い
AMは従来の除去加工とは発想が根本的に異なります。材料を必要な分だけ使用して積み重ねるという特性から廃材が少なく、複雑な形状や軽量構造の実現にも適しています。これにより、少量多品種・短納期といった現代の生産要求に柔軟に応えられる技術として注目されています。特に少量多品種やカスタム製品の生産が求められる現場では、従来工法では難しかった領域をカバーできる点が強みです。
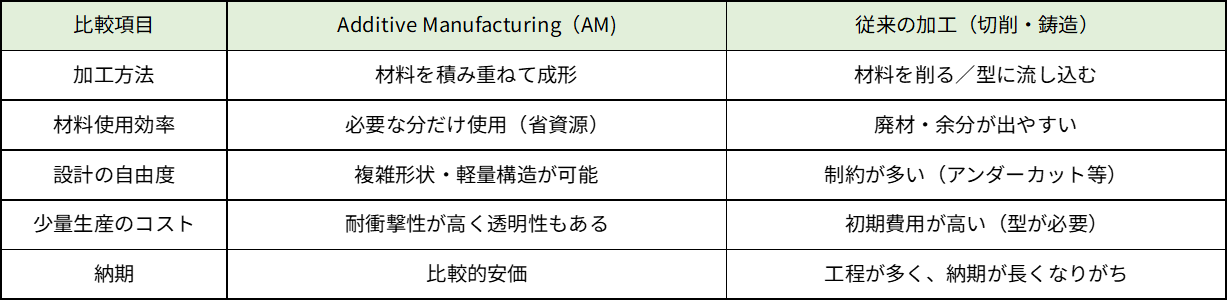
2. AMの主な種類と方式
AMには使用する材料や造形方法の違いによっていくつかの主要な方式があります。用途や必要な性能に応じて最適な方式を選択することが重要です。
FDM(熱溶解積層)はフィラメント状の樹脂をノズルで加熱・押出ししながら造形する手法で、最も普及しています。コストが低く扱いやすいために試作や簡易治具によく使われます。
SLA(光造形)は液体樹脂を紫外線で硬化させて積層する方式で、高精度な造形と滑らかな表面仕上げが特徴です。
SLS(粉末焼結)はナイロンなどの粉末材料をレーザーで焼結する方式で、複雑な形状や耐久性が求められる部品に適しています。
金属AMは金属粉末をレーザーや電子ビームで溶融・凝固させて造形する方式で、エンジン部品や金型など、実際の製品製造にも用いられています。
3. なぜ今、AMが注目されているのか
AMが近年とくに注目を集めている背景には、技術革新だけでなく製造業を取り巻くビジネス環境の大きな変化があります。ここではAMが現代の製造業において重要視される理由を4つの観点から整理します。
3-1. デジタル製造との親和性
AMは設計データ(CAD)から直接造形を行えるという特長があり、設計と製造がシームレスにつながる「デジタル製造」に最適な技術です。従来のように図面を紙でやり取りし、別工程で加工する必要がなくなることで開発サイクル全体が短縮されます。また、デジタルツインやIoTと組み合わせることで遠隔モニタリングやリモート製造といった高度な生産体制も構築可能です。
3-2. 少量多品種・短納期への対応力
AMは金型を使わずに製造ができるため、小ロットや単品の生産にも柔軟に対応できます。工程も少なく設計変更に対してスピーディに対応できるため、開発期間の短縮にもつながります。また、必要な数だけ造形するオンデマンド生産が可能で在庫リスクを減らせるのも大きな強みです。試作から本番までを短期間で回すことができ、変動の多い製品展開にも向いています。
さらに、材料の無駄が少ないことや分散生産との相性の良さから環境負荷低減や脱炭素の観点からも注目を集めています。
3-3. カスタマイズ製品への需要
市場ニーズが「個別対応」「パーソナライズ」へと移行する中、AMは一点ものやカスタム仕様の製造に適した手段として注目されています。スキャンデータや個別設計データを元に1つずつ異なる製品でも短納期で対応可能です。義手・義足・歯科装置など医療分野のほか、BtoC製品のオーダーメイド化や試作段階の細かな仕様調整にも活用されています。
3-4. 脱炭素・環境負荷低減の観点から
AMは環境配慮型の製造技術としても評価されています。材料を必要な分だけ積層するため廃棄物が少なく、従来の切削加工に比べて材料ロスを大幅に削減できます。さらに、データ送信による現地造形が可能なため製品の輸送を減らすことができ、CO₂排出量の抑制にも貢献します。こうした特徴からカーボンニュートラルやESG対応の一環としてAMを導入する企業も増加しています。
AMは単なる「新しい造形方法」ではなく、従来の製造工程では実現できなかった柔軟性とスピードをもたらす技術です。少量多品種の製品でも金型なしで対応でき、コスト効率の良い生産が可能になります。また、設計の自由度が高く、複雑な内部構造や中空形状も造形できるため、製品性能の向上や部品点数の削減にも貢献します。開発サイクルの高速化にも寄与し、納期短縮と競争力向上に直結します。さらに、必要なときに必要な分だけ製造できるという特性は在庫レス運用や分散生産体制の実現にもつながります。
4. Additive Manufacturingのメリット
AMは製造プロセスに革新をもたらす技術です。従来の加工方法では対応が難しかった多様なニーズに柔軟に応えることができる点から、導入による効果は多岐にわたります。ここではAMが実現する代表的な4つのメリットについて紹介します。
4-1. 少量多品種製造に強い
AMは金型を使わずに直接造形できるため、少量生産や一品モノの製造でもコストを抑えられます。従来工法ではロット数が少ないと割高になっていた製品もAMなら柔軟に対応可能です。試作・検証モデルから本番製品まで同じ設備で段階的に展開できるため、生産リードタイムと設備投資の両面で効率化が図れます。個別対応が求められる製品や頻繁な設計変更がある現場において特に効果を発揮します。
4-2. 設計の自由度が高い
AMは積層造形という特性上、従来の加工制約にとらわれずに複雑な形状をそのまま造形できます。たとえば、中空構造やアンダーカット、内部ラティス構造といった従来難しかった設計も再現可能です。また、複数部品を一体化する設計によって組立工程や部品点数を削減でき、品質やコストにも好影響をもたらします。設計者のアイデアをそのまま形にできる自由度の高さは製品開発の幅を大きく広げます。
4-3. 短納期対応が可能
デジタルデータを元に即座に造形できるAMは設計変更への追従性が高く、試作や修正のサイクルを高速化できます。また、金型が不要なことから製造開始までのリードタイムも短縮され、開発全体のスピードアップに寄与します。
ただし、注意すべきは「造形用のデータ作成には一定の時間とスキルが必要」な点です。モデリングや設計データの準備ができていない段階では短納期の恩恵を十分に活かせないこともあります。そのため、事前準備やデジタル化体制が整っている現場ほどAMのスピードメリットを最大限に引き出せると言えるでしょう。
在庫切れや急な仕様変更といった突発的なニーズにもデータが揃っていれば即対応できるため、AMは現場の柔軟性を高める選択肢となります。スピードが競争力に直結する現代において「準備を整えた上での短納期対応」は大きな武器となります。
4-4. 在庫レス・分散製造の実現
必要なときに必要な数量だけ製造できるAMは、従来の「作り置き・保管」から「オンデマンド生産」への転換を可能にします。これにより在庫コストや保管スペースの削減、さらには過剰生産のリスク回避にもつながります。また、造形データさえあればどこでも再現できるため、地理的制約のない分散型生産も実現可能です。災害時のバックアップや輸送コストの削減といった点でもAMの利点は際立ちます。
5. AMの活用が進む業界と事例
AMはすでに多くの業界で実用化されています。たとえば、製造現場では作業治具や検査治具の内製化に活用されており、現場改善サイクルを加速させています。また、自動車や航空宇宙分野では軽量で高強度な部品を一体化して造形することで、性能とコストを両立させた製品開発が進んでいます。
医療分野では、個別に最適化された義手・義足や歯科用部品などの患者ごとにカスタム対応が必要な製品にAMが威力を発揮しています。さらに、金型レスでの樹脂部品生産や修理部品のオンデマンド供給など、一般製造業においても導入が広がりつつあります。
6. AM導入時の課題と設計のポイント
AMは高いポテンシャルを持つ一方で導入にあたってはいくつかの壁も存在します。安定した品質を確保するにはAM特有の設計ルールや設備特性を理解して適切に運用する必要があります。現場でよく課題となる3つのポイントを紹介します。
6-1. 造形品質の安定化
AMでは材料の性質や積層方向、サポート材の設計といった複数の要素が造形結果に影響します。同じデータでも造形条件が異なれば強度や精度に差が出るため、品質のバラつきが起きやすい傾向があります。特に量産を見据えた場合には安定して同じ品質を保つための条件管理とトレーサビリティが欠かせません。造形設定や材料ロットの管理などのデータの蓄積と最適化が重要です。
6-2. 材料コストと装置選定
AMは金型レスで初期投資が抑えられる一方で使用する材料単価が高くなりがちです。特に金属粉末や特殊樹脂は高価であり、保管や再利用に関する配慮も必要です。また、装置ごとに対応できる材料や造形サイズが異なるため、用途に合った設備の選定も課題となります。コストだけでなく、技術者のスキルや運用体制を含めた総合的な視点で検討することが重要です。
6-3. 設計思想の転換(DfAM)
AMを効果的に活用するには「AM向けの設計」に切り替える必要があります。これをDfAM(Design for Additive Manufacturing)と呼び、従来の切削加工などとは異なる設計発想を求められます。たとえば、軽量化のためにラティス構造を使ったり、複数部品を一体化して造形する設計が該当します。AMの性能を最大限に引き出すには設計と製造の連携が不可欠であり、設計段階からAMを前提にした考え方が求められます。
7. ラピッドプロトタイピングとの違い
AMと混同されやすい概念としてラピッドプロトタイピング(RP)があります。RPは主に試作品を迅速に製作することを目的としており、設計段階での検証や確認に用いられます。現在もRPは製品開発初期段階で有効な手段として多くの現場で活用されています。
一方、AMは最終製品や機能部品の製造を含む広い概念であり、生産工程そのものを支える技術として位置づけられています。技術的には重なる部分があるものの、工程上の役割や導入の目的によって明確に使い分けられるべき概念です。
8. AM導入を成功させるために
AMは単に装置を導入するだけでは成果を上げにくい技術です。導入効果を最大化するためには、設計・製造・調達など複数の部門が連携して目的に応じた運用体制を構築することが重要になります。特に中小製造業においては、いきなりすべてを自社で完結させるのは現実的ではありません。以下に、AM導入を段階的に進める上で押さえておきたいポイントを紹介します。
8-1. 社内教育とパートナー選定
まず必要なのは、技術部門や設計担当者がAMの特性と設計思想を理解することです。従来の加工ベースの常識では通用しない場面も多く、誤った運用ではAMの強みを活かしきれません。そのためには外部の支援企業や教育機関と連携しながら、トレーニングや設計支援を受けることも選択肢になります。装置販売だけでなく、材料や設計ノウハウまで提供してくれるパートナーの存在が導入初期では非常に大きな支えになります。
8-2. 試作から量産へ移行するステップ
初期導入では、まずは試作や簡易治具の内製化などのリスクの少ない領域から小さく始めるのが効果的です。設計〜造形〜評価までの一連の流れを自社で体験し、AMならではの勘所を掴むことで次のステップへの準備が整います。その後、製品の一部部品や限定的な数量での生産を試し、品質やコストのバランスを見ながら本格的な量産導入へと進めるのが理想的です。
8-3. 外注・受託製造の活用
装置や人材への投資を最小限に抑えながらAMを活用したい場合は、外注サービスや受託製造企業を活用するのが有効です。特に金属AMや高機能樹脂といったハイエンドな造形では、専門業者との協業によって品質を担保しながらスピーディに製品化が可能になります。設計支援から造形・後処理まで一貫して対応できるパートナーを活用すれば自社の製造能力を補完しながらAMを柔軟に取り入れることができます。
9. まとめ
AMは3Dプリント技術の進化とともに「試作」から「本番製造」へと活用領域を広げ、今や製造業にとって無視できない選択肢のひとつとなっています。
従来の製造方法に代わる技術ではなく、それらと併用・補完しながら新しい製品開発・供給体制を築いていくのがAMの本質的な価値です。特に少量多品種、短納期、柔軟な設計が求められる製造環境ではAMは強力な武器となります。
とはいえ、技術的な特性や設計上の前提、導入体制まで踏まえた運用が求められるため、いきなりすべてを内製化する必要はありません。まずは自社の課題に合った範囲で小さく導入し、社内の理解とノウハウを積み上げていくことが成功への第一歩です。
造形委託・設計相談など、お困りのことがあればお気軽にご相談ください。3Dプリントを活用した製造の現場づくりを私たちがお手伝いします。
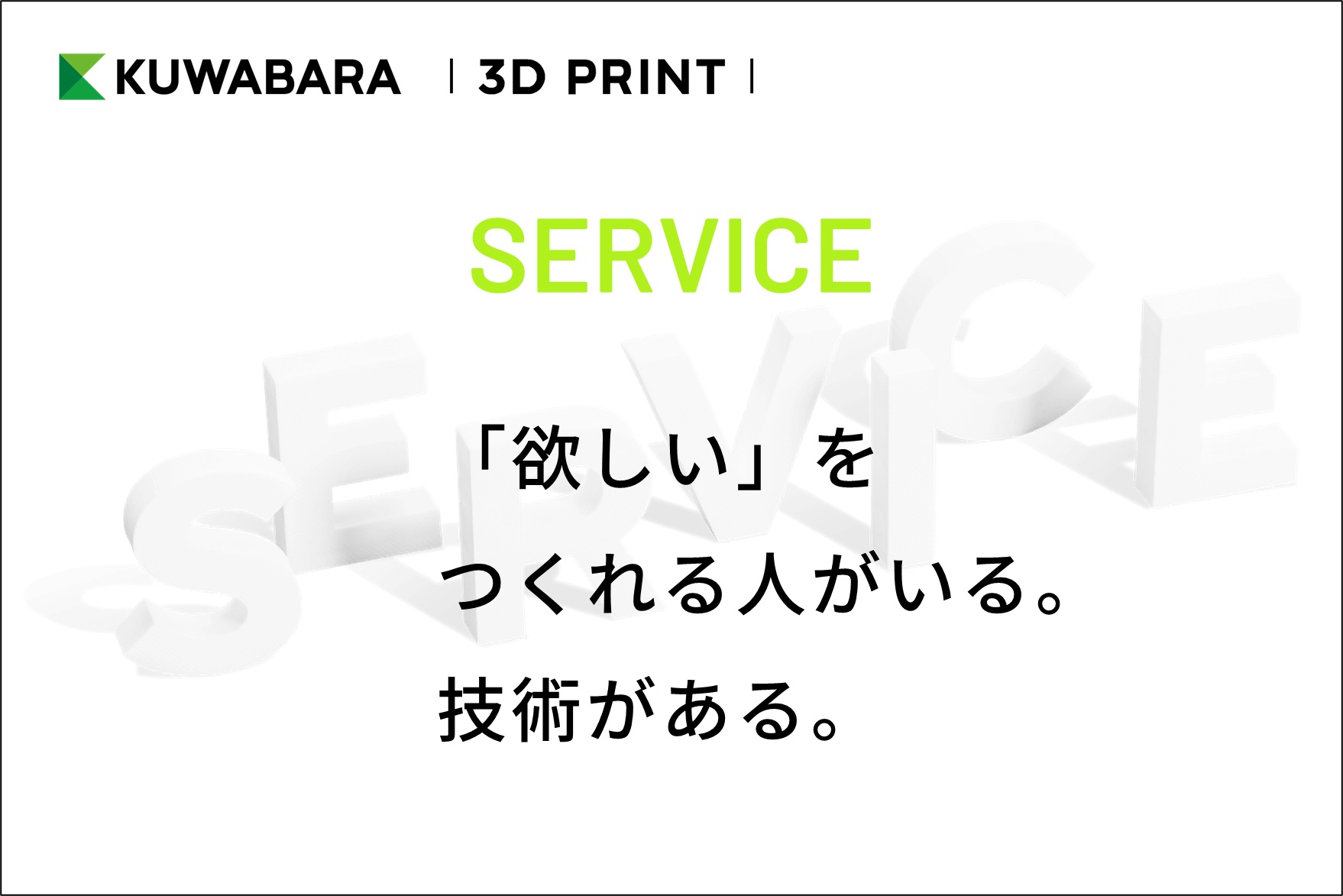
KUWABARA 3D PRINTご利用の流れはこちら
https://www.kuwabara-3d.com/service/