2025.7.17
複雑形状の部品はどう作る?3Dプリントを活用した製作方法と設計の考え方
機械部品や機能部材の設計において、「構造が複雑すぎて製作できない」「分割して組み立てるしかない」といった悩みは多くの設計現場で発生しています。軽量化・高性能化が進むなかで、内部に流路を持つ中空形状や、微細なラティス構造、一体化された支持構造など、省エネ性能や熱伝達効率の向上を意図した設計が増え、これまで以上に複雑な構造が求められています。
従来の加工法では対応が難しかったこれらの形状も、3Dプリント(積層造形)の進化によって製作可能なケースが増えています。本記事では、複雑形状の意味と背景を整理しつつ、3Dプリントを活用するための設計と製作の考え方を分かりやすく解説します。
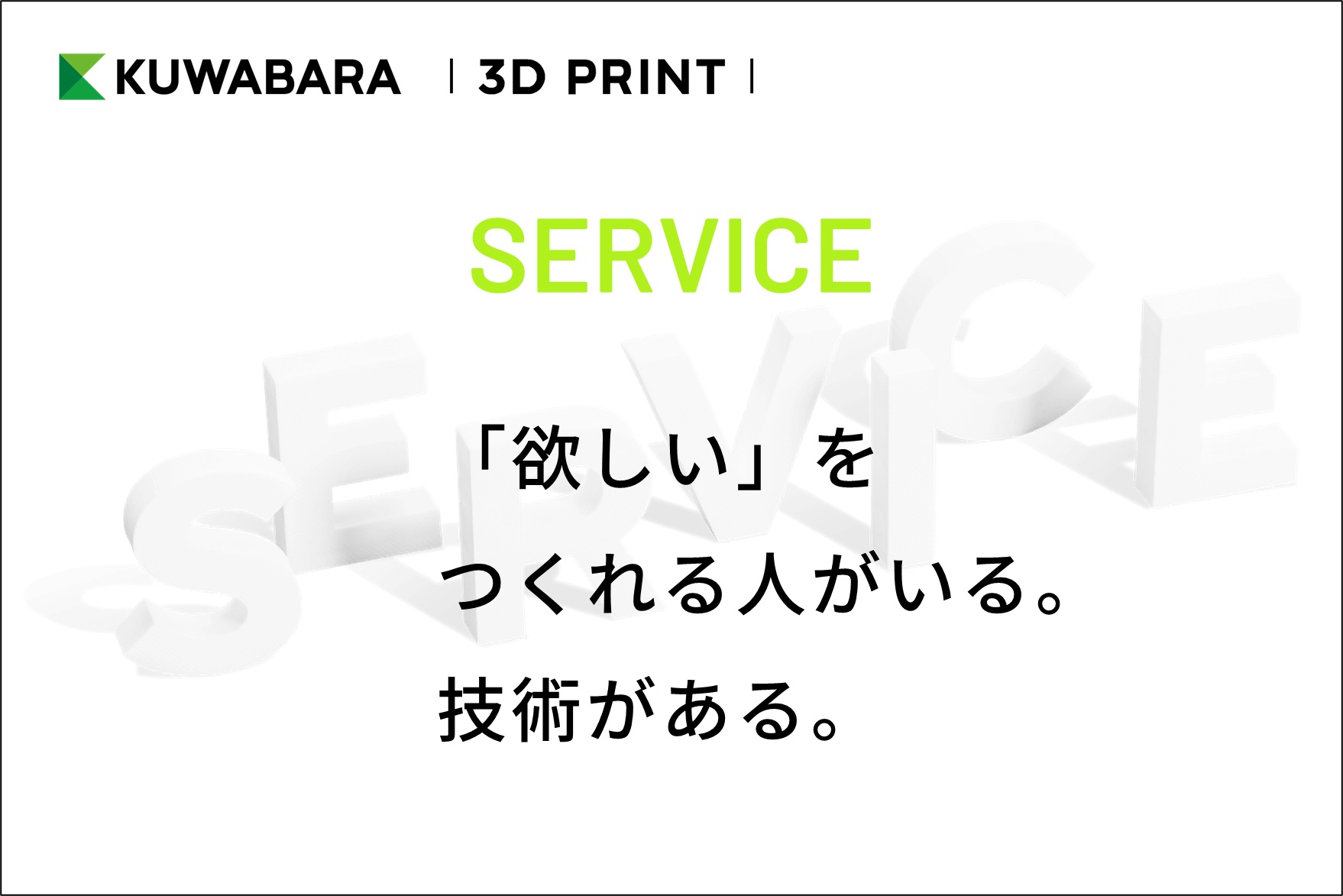
「複雑形状を3Dプリントで製作するには、どのような流れで依頼すればよいのか?」という方へ。弊社サービスページにて、設計検討から造形・納品までのプロセスをご案内しています。
https://www.kuwabara-3d.com/service/
目次
1. 複雑形状とは?製造現場で求められる背景と事例
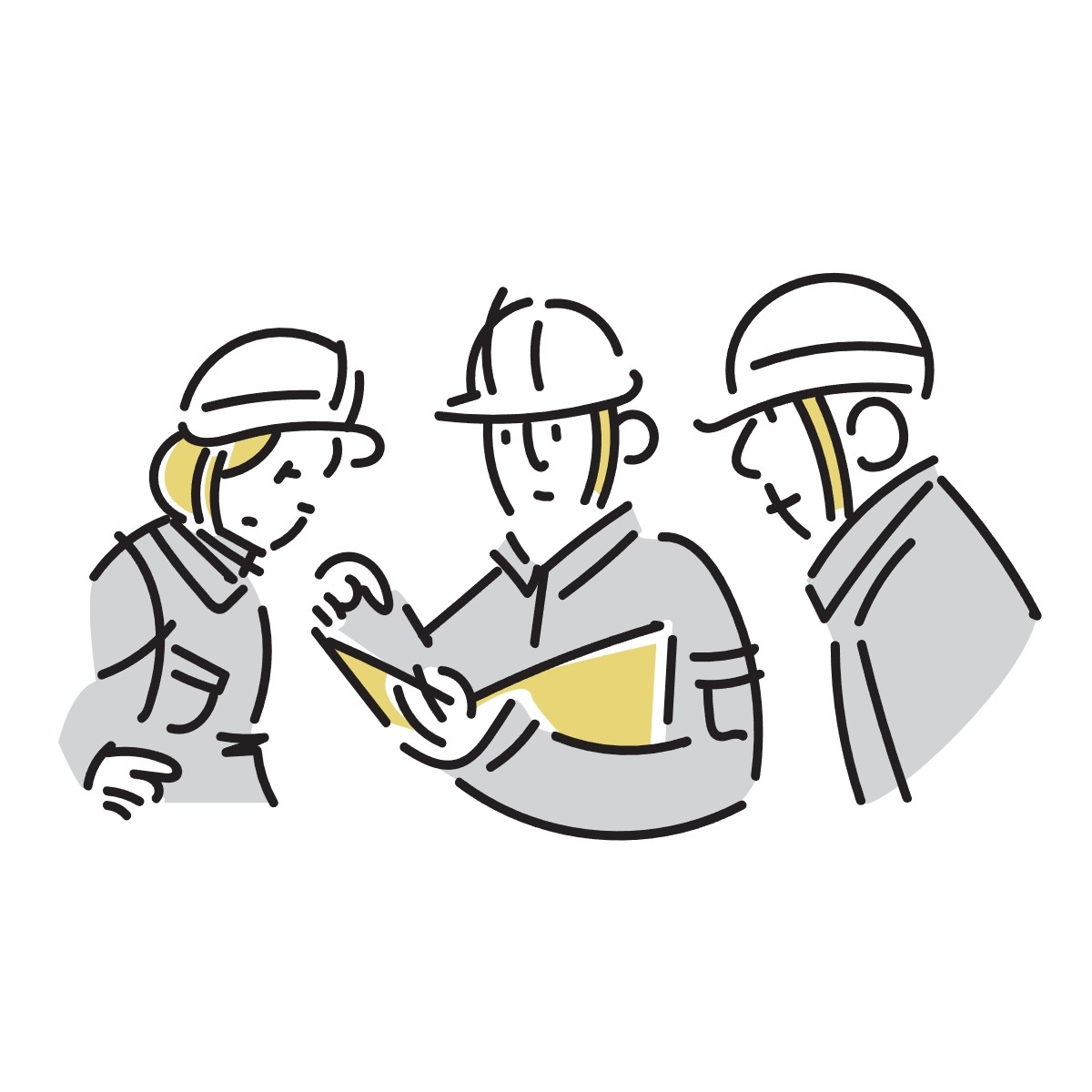
製造現場では今、軽量化・高機能化・省スペース化といった要求の高まりにより、これまでにない複雑な構造を持つ部品が求められています。設計者は構造上の制約を乗り越え、複数の機能を一体化したり、最小限の材料で最大限の性能を引き出したりする工夫を迫られています。そうした設計を実現するには、製造プロセスとの整合も欠かせません。ここでは、なぜ複雑形状が必要とされているのか、そしてどのような形状がその代表例となるのかを整理します。
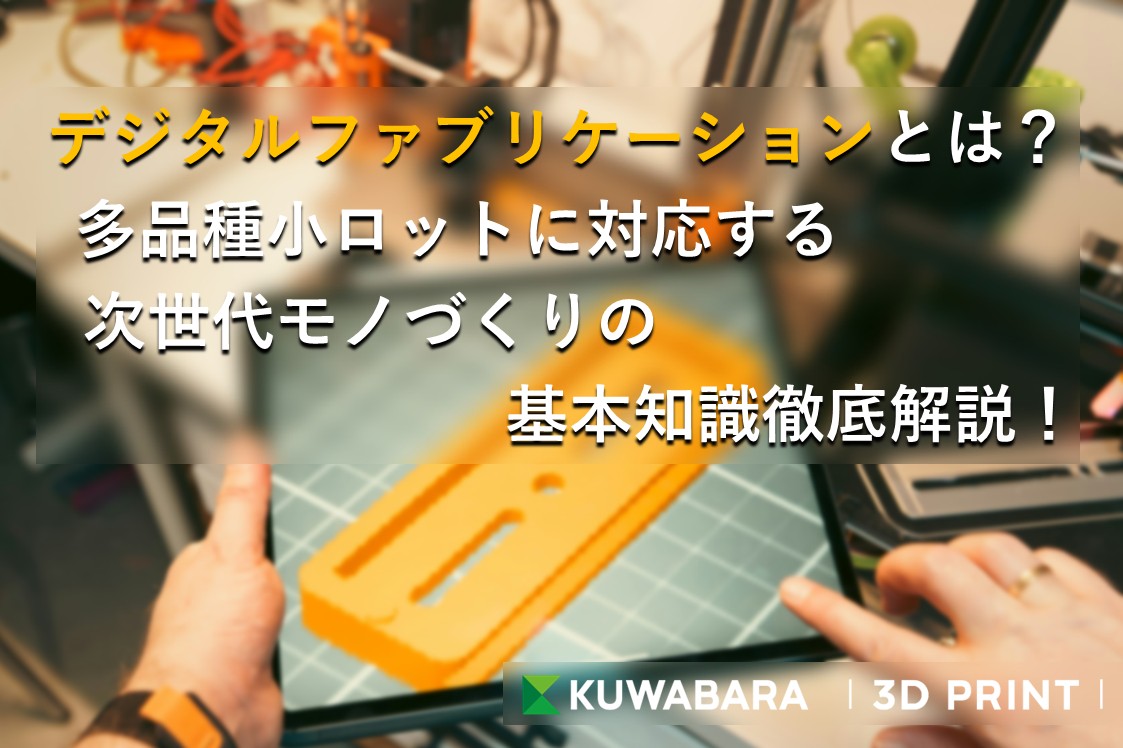
製造プロセスとの整合も欠かせません。こうした柔軟な設計と生産を実現する新しい考え方として、デジタルファブリケーションの概念も注目されています。
デジタルファブリケーションとは?多品種小ロットに対応する次世代モノづくりの基本知識
https://www.kuwabara-3d.com/column/c015/
1-1. 複雑形状が必要とされる理由
複雑形状が注目される背景には、機能性と生産性の両立が求められる現場事情があります。例えば、軽量化は省エネや可搬性向上に直結し、航空・自動車・ロボット分野では特に重要です。また、異なる機能を一体化することで部品点数を削減でき、組立工数やトラブルリスクの低減にもつながります。さらに、内部構造の工夫によって冷却効率を高めたり、流体の制御性を高めたりするケースも増えています。製品性能を高めながら、生産性も維持する手段として、複雑形状はますます重要な設計要素となっています。
1-2. 複雑形状の代表例と課題
複雑形状とされる代表的な例には、ラティス構造、中空形状、アンダーカット、内部流路などがあります。ラティス構造は軽量でありながら高い剛性を持ち、航空部品や医療用インプラントでの応用が進んでいます。中空形状や内部流路は冷却や流体制御のために設計されますが、従来加工では実現が困難でした。アンダーカットを含む形状も、マシニングや金型では成形が難しく、分割や後加工が避けられません。こうした形状は、設計段階から加工制約を踏まえた手法の選定が不可欠です。
2. 複雑形状に対応できる加工方法の比較
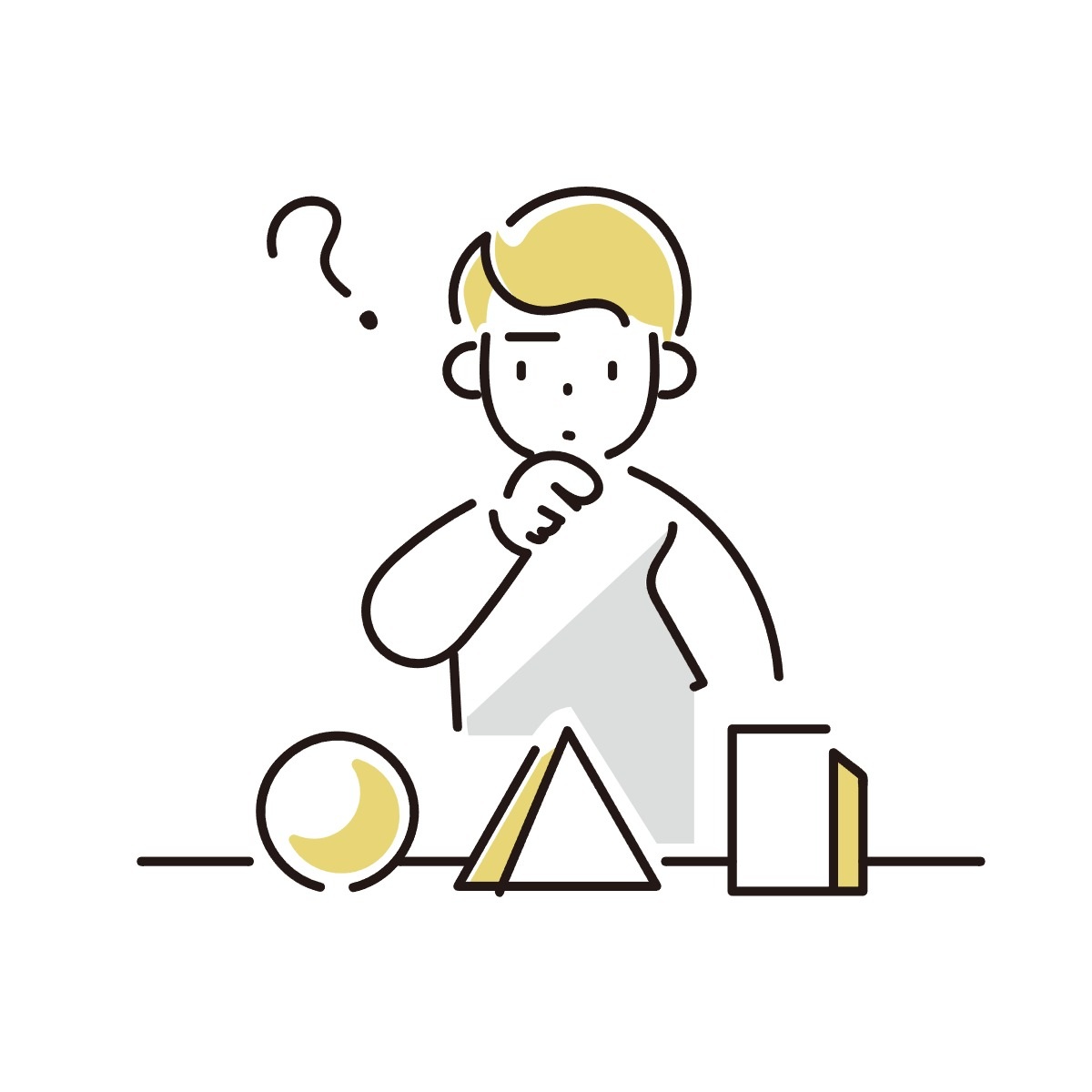
複雑な構造をもつ部品を製作する際、どの加工方法を選ぶかはコスト・納期・精度に大きく影響します。切削、鋳造、射出成形といった従来の工法でも複雑形状への対応は可能ですが、それぞれに形状制約や工程上の限界があります。一方、近年注目されている3Dプリントは、設計の自由度を大きく広げる選択肢となっています。この章では、代表的な加工方法ごとに複雑形状への対応力やメリット・デメリットを比較し、最適な工法選定のヒントを探ります。
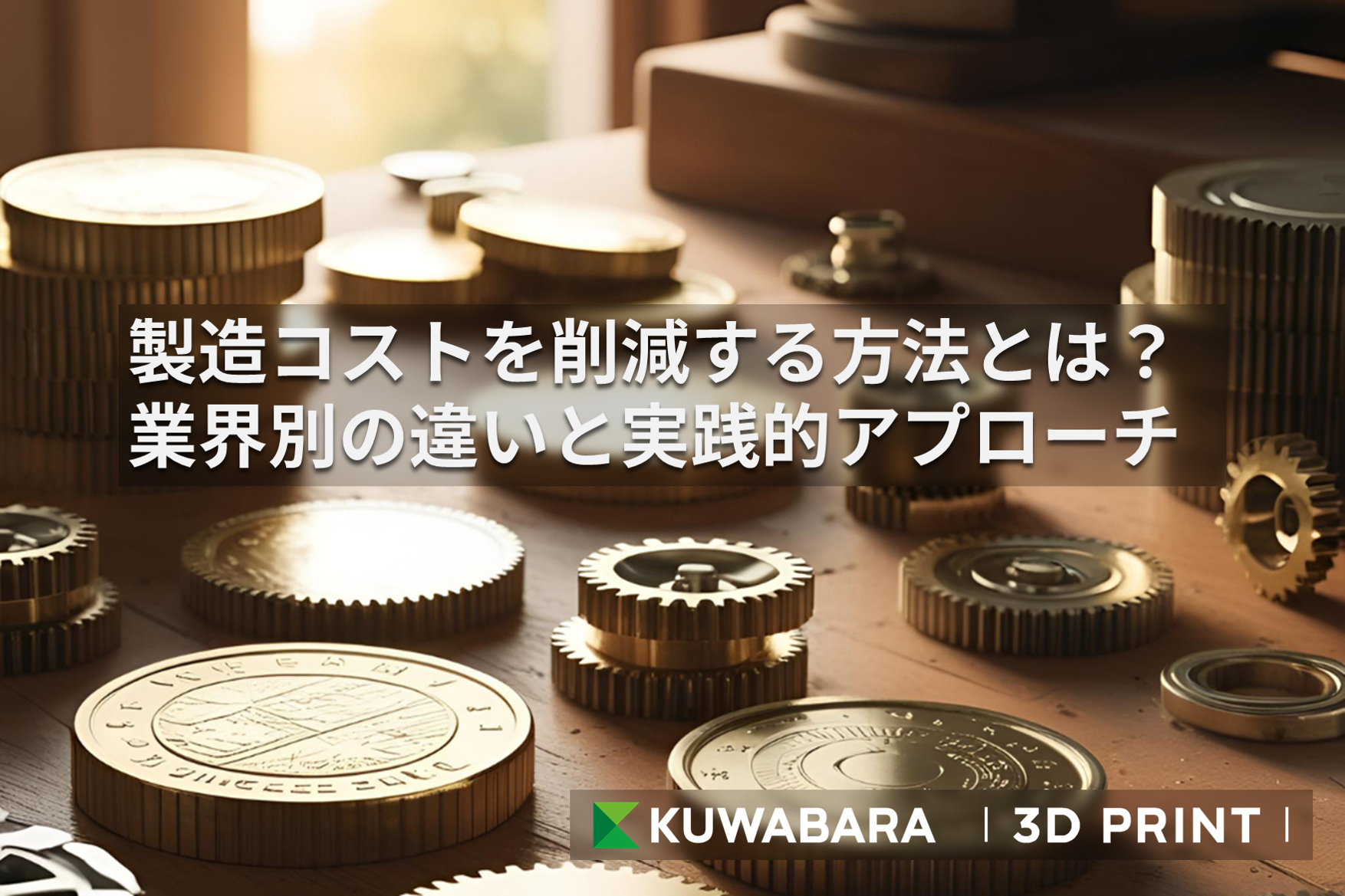
加工方法の選定は形状の実現性だけでなく、製造コストにも大きく関わります。各方式のコスト構造や削減策については、こちらの記事も併せてご覧ください。
製造コストを削減する方法とは?業界別の違いと実践的アプローチ
https://www.kuwabara-3d.com/column/c013/
2-1. 切削加工|高精度だが形状制限あり
切削加工(マシニング)は高精度で信頼性の高い加工法として広く用いられていますが、工具が物理的にアクセスできる範囲に限られるため、アンダーカットや内部空間を含む形状には不向きです。複雑な構造を製作するには、分割加工や冶具の工夫が必要になり、工程数やコストが増加します。また、細く複雑な内部構造は加工中の破損リスクも高く、設計段階で形状の簡略化を余儀なくされることも少なくありません。精度の高さは魅力ですが、自由な形状設計には明確な制約が伴います。
2-2. 鋳造・ロストワックス法|複雑形状に強いが工程が多い
鋳造やロストワックス法(精密鋳造)は、複雑な曲面や空間構造の再現が比較的得意な加工法です。とくにロストワックス法では、柔軟なWAX型を用いることでアンダーカットや中空構造を表現することができます。ただし、型の製作や焼成、鋳込みといった工程が多く、短納期対応や少量生産には向いていません。内部流路や一体成形を実現するには中子設計などの高度なノウハウも必要です。高機能形状に対応できる一方で、多工程によるコスト増が課題となります。
2-3. 射出成形|量産向きだが金型制約が大きい
射出成形は、量産性に優れた成形方法としてプラスチック部品を中心に広く使われていますが、複雑形状の対応には大きな制約があります。主な制約は金型の構造に由来し、アンダーカットや中空構造にはスライド金型や可動中子が必要となり、設計・製作コストが跳ね上がります。また、金型自体が高価なため、少量生産には不向きです。一体化構造や複雑な内部構造の実現には限界があり、設計の自由度は限定的です。射出成形は、あくまで「形が固まった量産向け」の工法といえます。
2-4. 3Dプリント(積層造形)|自由形状対応・一体成形が可能
3Dプリントは、複雑形状への対応力が極めて高い加工技術です。従来の加工法で制約となっていたアンダーカット・中空構造・流路・一体成形なども、積層方向とサポート材の設計によって再現可能になります。さらに、設計から製作までがデジタルで完結するため、試作や少量生産にも柔軟に対応できます。部品点数削減・軽量化・機能統合といった設計上のメリットをそのまま形にできるため、近年ではトポロジー最適化やジェネレーティブデザイン(AIが設計条件に応じて無数の形状案を自動生成する手法)と組み合わせた活用も進んでいます。
3. 3Dプリントが得意とする複雑形状の特徴
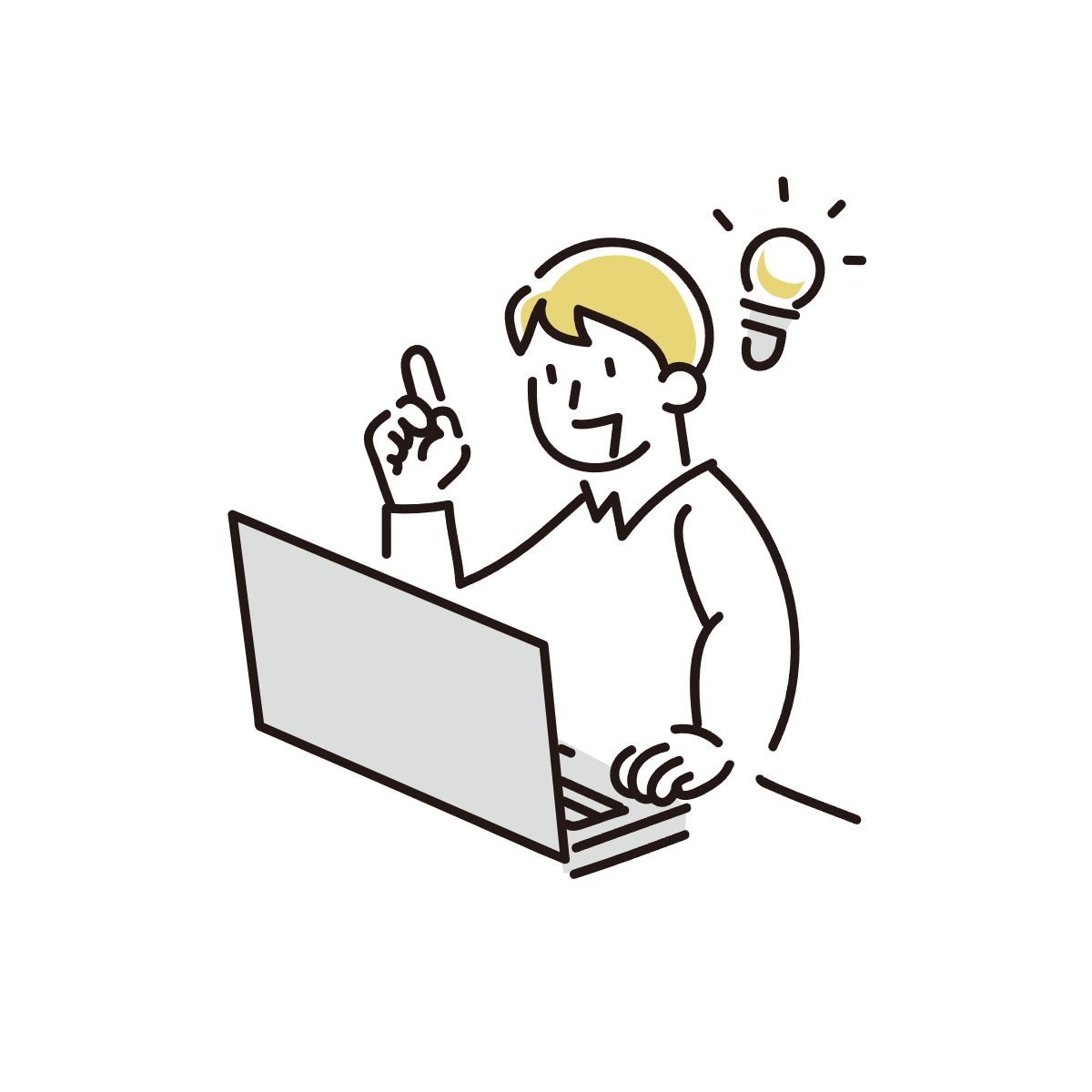
従来の加工法では、製造都合で設計に制約がかかる場面が多くありました。しかし3Dプリント(AM:Additive Manufacturing)は、積層による造形特性を活かし、設計の自由度を大きく広げる技術です。特に複雑形状においては、金型や工具の制約を受けずに造形が可能なため、ラティス構造や内部流路、アンダーカット、一体成形といった形状も現実的に製作できます。この章では、3Dプリントが真価を発揮する代表的な複雑形状の特徴を取り上げ、それぞれの活用価値を解説します。
3-1. ラティス構造|軽量化と剛性を両立
ラティス構造とは、格子状に組まれた中空構造のことで、軽量性と高い剛性を両立させる設計に用いられます。従来の加工法では製作が極めて困難でしたが、3Dプリントなら数ミリ以下の微細な構造でも再現可能です。これにより、航空機部品や医療用インプラント、産業機器の構造部などで、重量を抑えつつ必要な強度や弾性を確保する設計が可能になります。また、設計段階で任意の密度・形状を持たせることができるため、機能最適化と材料削減を両立できる点でも注目されています。
【参考文献】AM技術のマイクロラティス構造への活用(牛島 邦晴・長倉 祐太・吉村 彰記)
https://www.jstage.jst.go.jp/article/jspmee/6/3/6_125/_pdf/-char/ja
3-2. アンダーカット・複雑な曲面|金型レスで実現可能
アンダーカットや複雑な曲面は、従来の切削や成形では「避けるべき形状」とされてきました。これは工具の干渉や金型からの抜き方向に制限があるためです。3Dプリントではこの制約が大きく緩和され、積層方向を工夫したり、サポート材を活用することで複雑な形状の再現が可能になります。美術・建築模型や流体制御部品など、曲面や裏面形状の多いパーツでも形状変更なしに一体成形でき、設計の自由度を飛躍的に高めることができます。
3-3. 内部流路・空洞形状|流体制御や冷却構造に有効
3Dプリントの最大のメリットのひとつが、外部から見えない内部構造をそのまま一体で造形できる点です。これにより、部品内部に複雑な流路を設けて冷却液や空気を通したり、重量を軽減するための空洞を仕込んだりといった設計が可能になります。従来の加工法では、中子や分割構造が必要だったため、工程や精度に課題がありました。
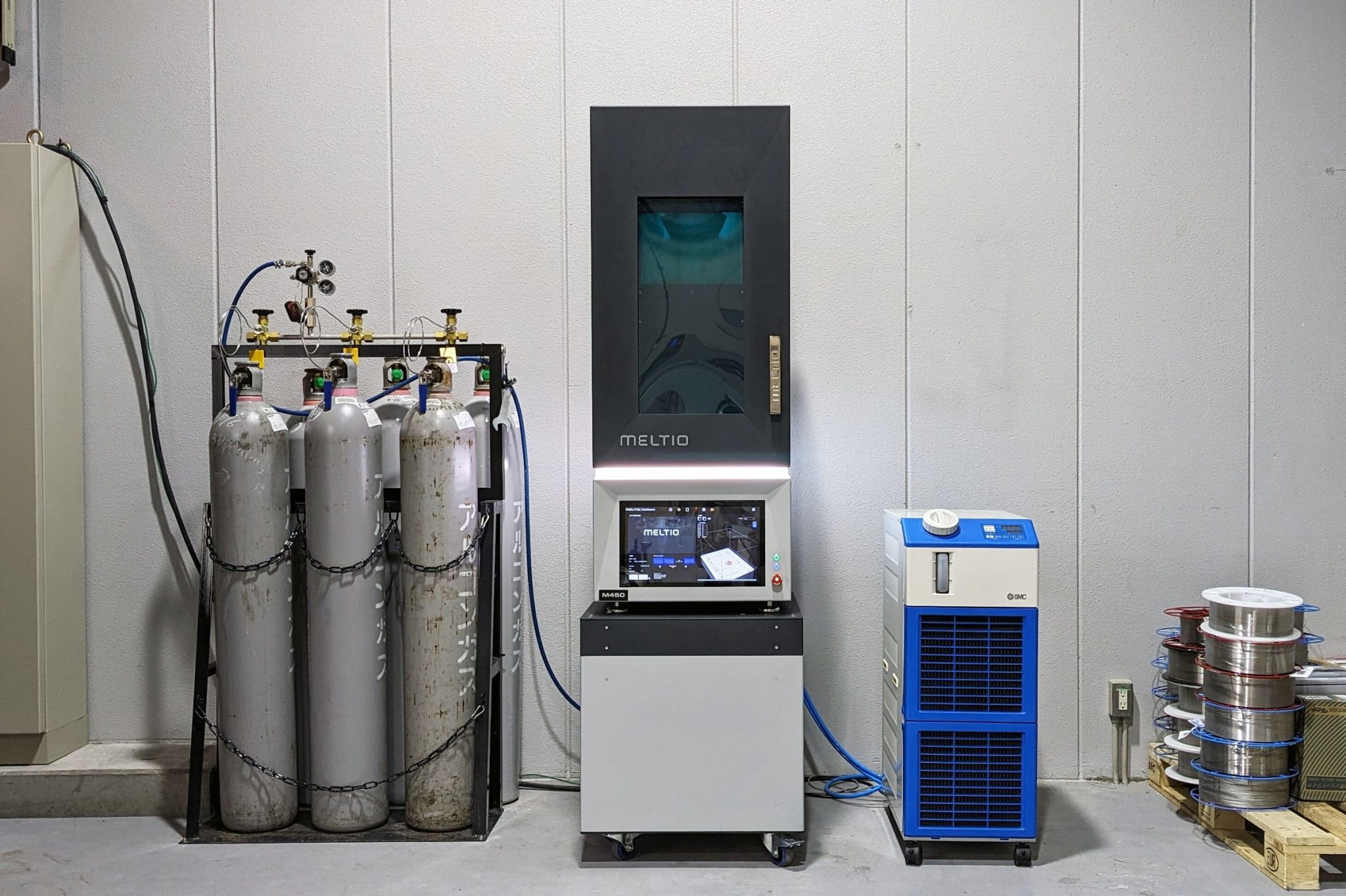
たとえば、射出成形用の金型に3Dプリントで3次元の冷却流路を組み込むことで、冷却時間を大幅に短縮した事例もあります。
3次元水管によって、射出成形の冷却時間を半減。
https://www.kuwabara-3d.com/works/20241107c/
こうした内部構造の工夫によって、流体制御・放熱・圧力損失の最適化といった高機能設計も、少量から短納期で実現できます。
3-4. 一体成形構造|部品点数削減・強度向上
複雑形状を一体で造形できるという3Dプリントの特性は、部品点数の削減にも大きく貢献します。従来は複数部品を分割設計・組立していた機構も、設計次第で一体化できるため、ねじ止めや接着といった工程を省略できます。これにより、製造工数・組立誤差・部品在庫の削減といった効果が得られるだけでなく、構造的にも継ぎ目のない高強度な部品を実現できます。設計と製造を統合的に見直すうえで、3Dプリントによる一体成形は大きな設計革新の手段となります。
【参考文献】 アディティブマニュファクチャリングによる複雑部品の製作と設計製造の分散化(舘野 寿丈)
https://www.jstage.jst.go.jp/article/isciesci/61/3/61_95/_article/-char/ja/
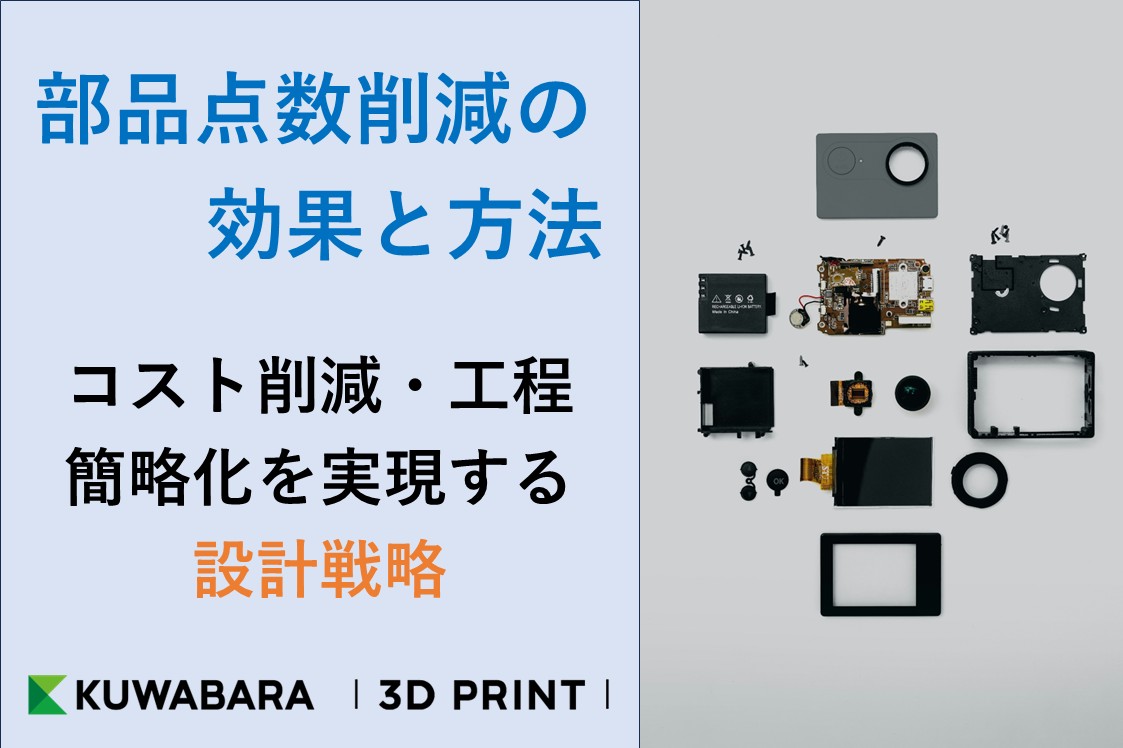
部品点数削減による設計・製造の効率化については、以下の記事でも詳しく解説しています。
部品点数削減の効果と方法|コスト削減・工程簡略化を実現する設計戦略
https://www.kuwabara-3d.com/column/c009/
4. トポロジー最適化と3Dプリントの相性
複雑形状の設計は、単に形を作るだけでなく「最適な構造をどう実現するか」という視点も重要です。特に近年は、解析結果をもとに材料配置を自動生成する「トポロジー最適化」や「ジェネレーティブデザイン」が注目されており、3Dプリントとの組み合わせによって革新的な設計と製造が可能になっています。この章では、従来では実現困難だった最適形状を、いかにして3Dプリントによって具現化できるのか、その仕組みと活用事例の方向性を紹介します。
4-1. 従来設計では再現困難だった形状がそのまま造形可能に
トポロジー最適化とは、必要な荷重や剛性などの条件を与えたうえで、構造に必要な最小限の材料配置を解析により導き出す設計手法です。しかし、最適化された形状は複雑で有機的な曲面や空洞を含むことが多く、従来の加工法では実現が難しいものでした。3Dプリントを活用すれば、これらの形状をそのまま造形可能となり、機能から逆算した形状設計を製品として具現化できます。設計と製造の一体化により、性能向上と部品最適化を同時に達成することができます。
【参考文献】はじめてのトポロジー最適化(大阪大学 矢地 謙太郎)
https://www.jstage.jst.go.jp/article/jjspe/85/11/85_965/_pdf
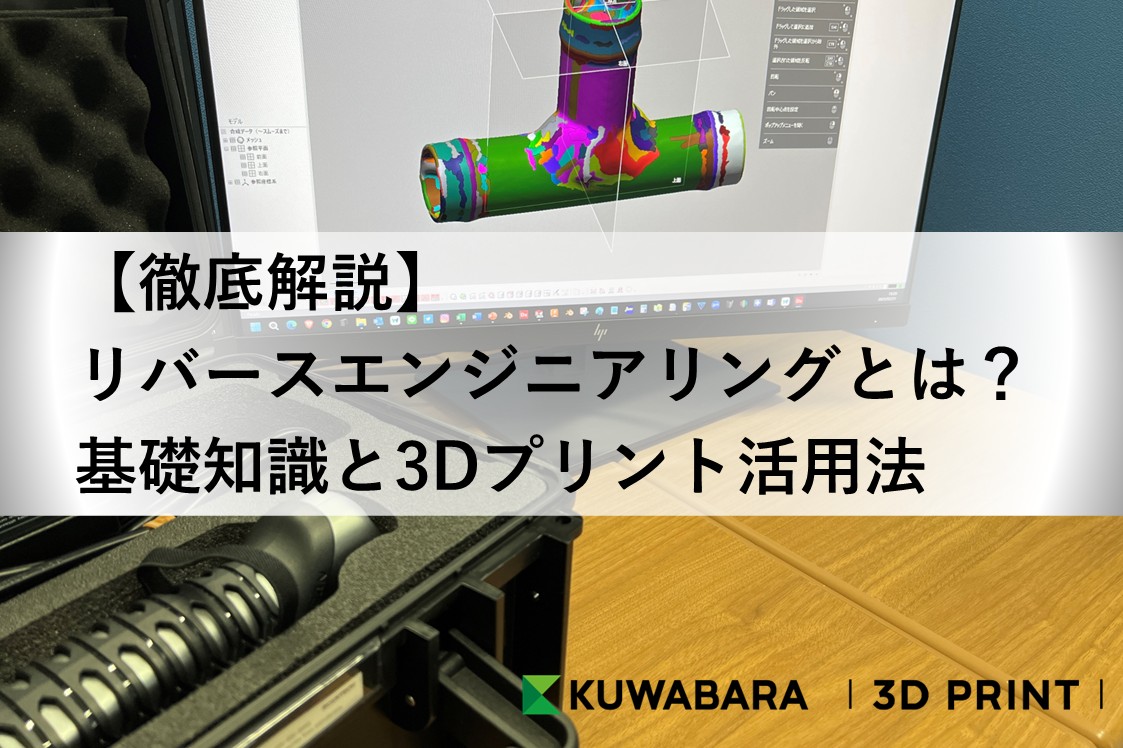
設計対象が既存部品である場合には、スキャンデータを活用して設計最適化する方法もあります。
【徹底解説】リバースエンジニアリングとは?基礎知識と3Dプリント活用法
https://www.kuwabara-3d.com/column/c005/
4-2. ジェネレーティブデザインとの連携による活用例
ジェネレーティブデザインは、設計者が定めた目的・制約・素材・荷重条件などをもとに、AIが数百〜数千の設計案を自動生成する革新的な設計手法です。この中で最適な案を選び、3Dプリントによって直接形状化することで、人の発想を超えた構造を製品に落とし込むことが可能になります。特に航空・モビリティ・医療分野では、軽量化と高性能の両立を目指した設計が進んでおり、ジェネレーティブデザインと3Dプリントの組み合わせは、今後の製品開発における重要なアプローチのひとつです。
【参考文献】ジェネレーティブデザインを活用したディーゼルエンジンのギア構造最適化(山岸 誠弥・岡崎 一也・石川 泰裕・山下 健一)
https://www.jstage.jst.go.jp/article/jsaeronbun/56/1/56_20254029/_pdf
5. 複雑形状を3Dプリントで製作する際の注意点
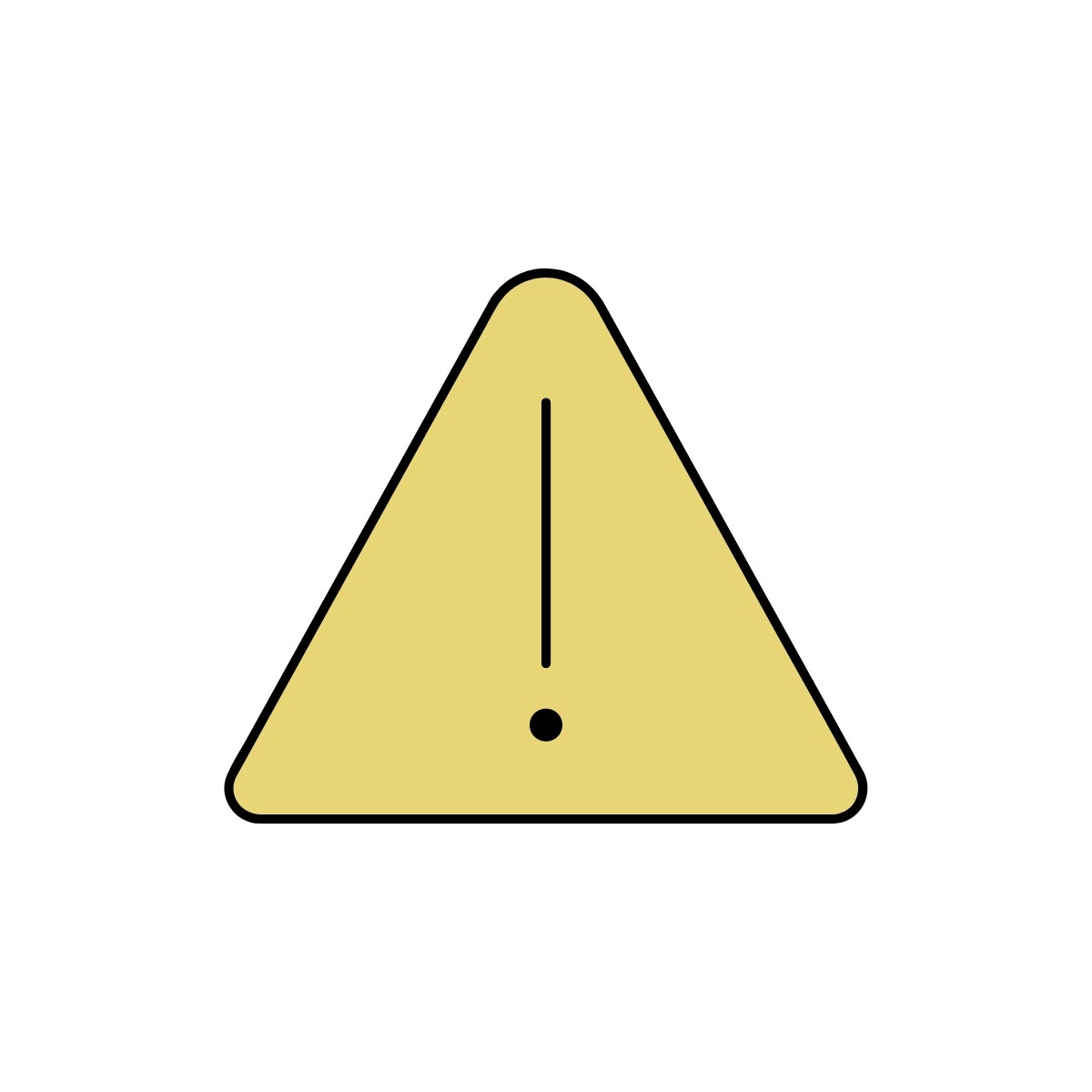
3Dプリントは複雑形状の造形に優れた手法ですが、万能ではありません。設計の自由度が高い分、造形方式や材料の選定、サポート構造の配置など、事前に考慮すべき要素も多く存在します。材料や方式の選定を誤ると、品質の低下や造形失敗の原因になります。本章では、複雑形状を3Dプリントで製作する際に押さえておきたい基本的な注意点について、設計面・技術面の両方から解説します。
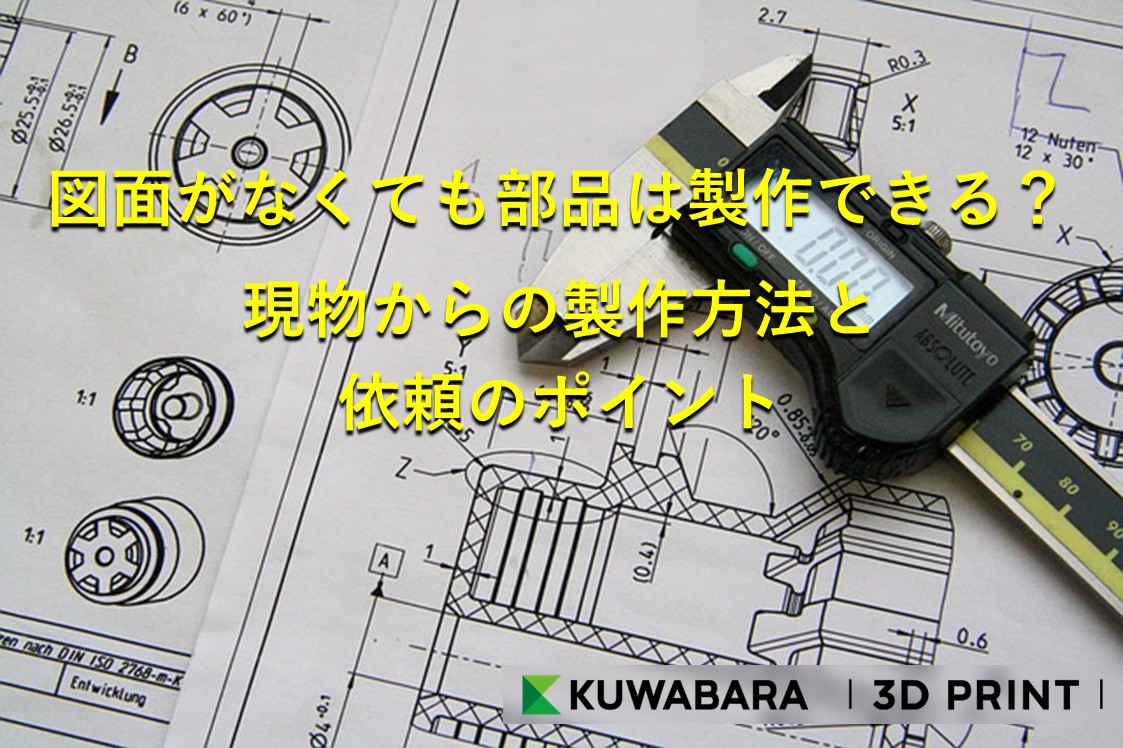
設計図が用意できない場合でも、対応可能なケースもあります。
図面がなくても部品は製作できる?現物からの再現方法と依頼のポイント
https://www.kuwabara-3d.com/column/c016/
5-1. 対応する造形方式と材料の選び方
複雑形状を造形する際には、適した方式と材料を選ぶことが成功の第一歩です。たとえば微細なラティスや薄肉形状には高精度なSLA(光造形)やMJF(材料噴射)方式が適しており、大型・中空構造にはFDM/FFF(熱溶解積層)やSLS(粉末焼結)方式が向いています。材料も、樹脂・金属・ゴムライクなど多様な特性があるため、使用環境や強度要求に応じた選定が必要です。設計と材料・方式の特性を正しくマッチングさせることで、意図した性能を確保できます。
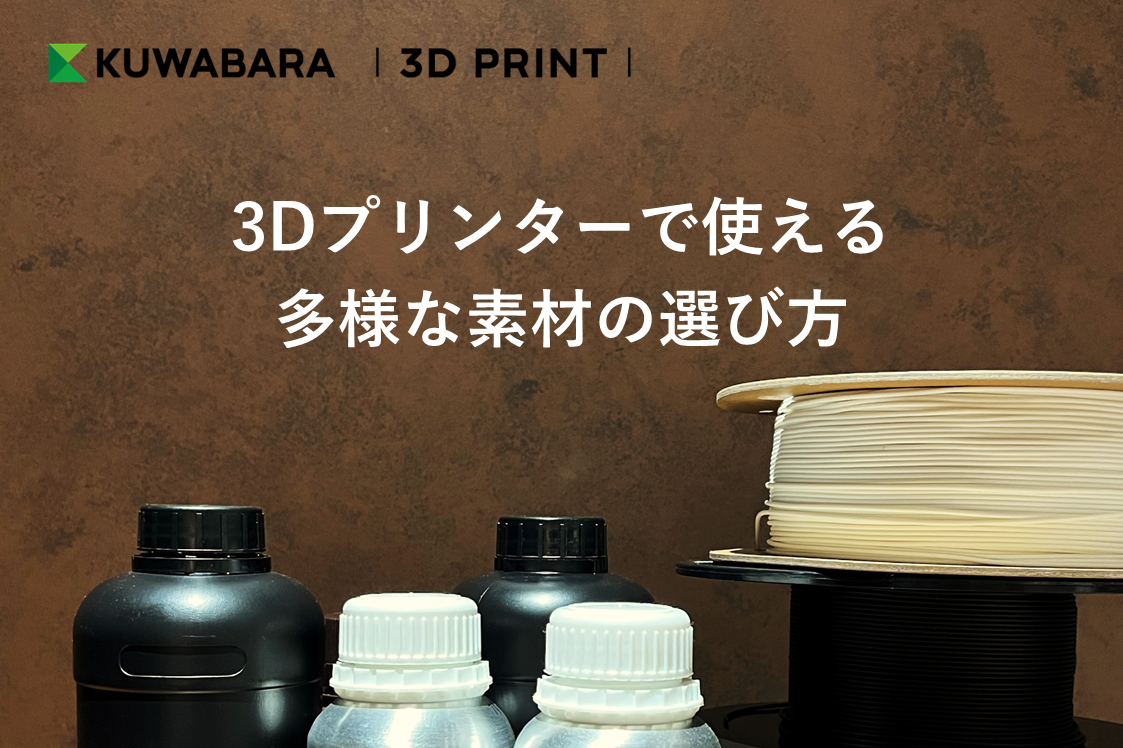
使用できる材料の種類や特性について詳しく知りたい方は、以下の記事もご参照ください。
3Dプリンターで使える多様な素材の選び方
https://www.kuwabara-3d.com/column/c001/
5-2. DfAM(3Dプリント設計最適化)で注意すべきポイント
DfAM(Design for Additive Manufacturing)は、3Dプリントに最適化された設計手法のことを指します。複雑形状を効果的に出力するには、単に3Dモデルを作るだけでなく、積層方向・肉厚・フィレット処理・サポートの配置などを考慮する必要があります。また、鋭すぎるエッジや極端な薄肉は、造形エラーの原因となることがあります。DfAMの考え方を取り入れることで、品質・造形成功率・後処理の容易さを大きく向上させることができます。
5-3. サポート材と後処理の影響
複雑形状の造形では、サポート材の配置と後処理のしやすさも重要な要素です。特にアンダーカットやオーバーハング部は、造形中に形状を維持するためにサポート材が必要になりますが、この配置によって仕上がり精度や表面性状に影響が出ることがあります。さらに、サポート材の除去には手作業や溶解処理が必要となる場合もあり、設計段階から取り外しやすさを意識することが求められます。サポート材は不可欠な要素であると同時に、仕上がりを左右する設計要因でもあります。
6. まとめ|複雑形状の製作は3Dプリントでさらに自由に
複雑形状の部品は、従来の加工法では製作が難しく、設計側も制約に悩まされてきました。3Dプリントの登場によって、ラティス構造や内部流路、アンダーカット、一体成形といった形状も現実的に造形可能となり、設計の自由度は大きく広がっています。とはいえ、方式や材料の選定、サポート設計といった要素には専門的な判断も必要です。弊社では、設計データの段階から造形可否の検討、最適な造形方式の選定、試作まで対応可能です。造形可否の判断に迷った際や、最適な加工方法を検討したい場合も、お気軽にご相談ください。